GMP Remediation: A Risk-Based Approach
- Mar 13
- 3 min read
Managing a major GMP remediation project is more than just responding to regulatory findings.
It’s about identifying true compliance risks, prioritizing actions effectively, and implementing solutions that create lasting change. Many companies struggle with remediation because they treat all issues as equally urgent, spreading resources too thin and focusing on symptoms instead of root causes.
A well-structured remediation effort requires a site-approved Quality Remediation Plan (QRP) that outlines clear actions, deadlines, and priorities. This plan ensures that remediation is not only effective but also documented in a way that regulators expect.
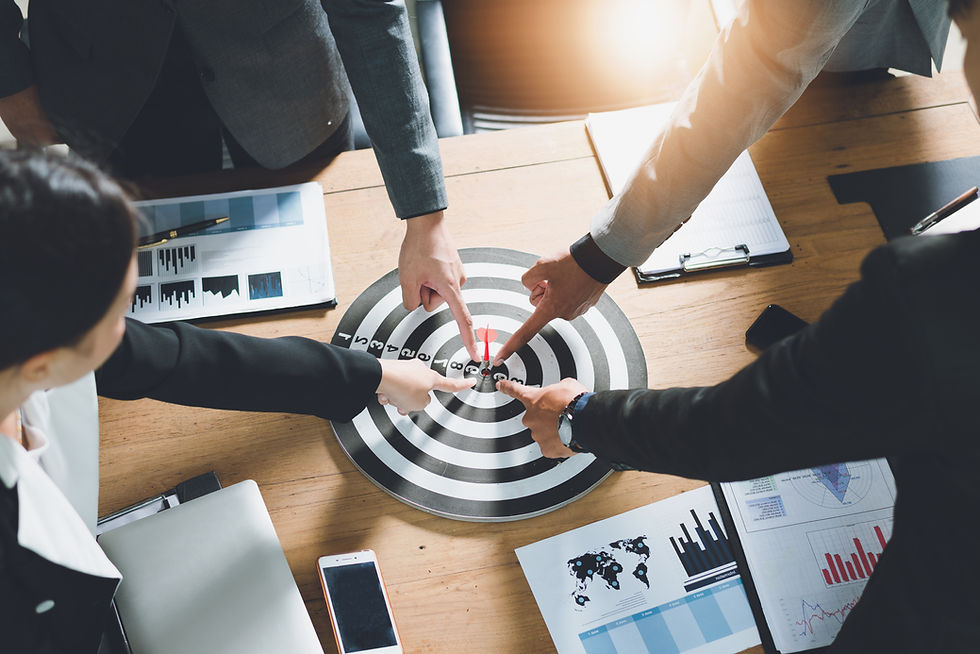
Risk-Based Remediation: Focusing on the Right Issues
Not all compliance gaps carry the same level of risk. Some findings, if left unaddressed, could lead to product recalls, supply chain disruptions, or regulatory enforcement, while others may pose lower operational risks and can be resolved over time.
A structured, risk-based remediation plan helps organizations focus on:
Immediate risks to patient safety and product quality
Regulatory concerns that could trigger enforcement action
Systemic issues that may lead to repeated failures
The Quality Remediation Plan (QRP) serves as a central document to define remediation actions, set clear timelines, track progress, and provide transparency for auditors.
This plan outlines:
The risk level of each compliance gap
Corrective and Preventive Action (CAPA) plans to ensure sustainable fixes
A structured implementation timeline with clear milestones
Accountability for execution across teams
Defining Remediation Priorities
Once you have identified all your risks, you need to prioritise your remediation activities. These can be tackled as individual workstreams with the relevant expertise leading each function, these could include:
1. Facilities, Utilities, and Equipment
Remediation CAPA actions might include:
✔ Replacing outdated utility systems to maintain environmental control
✔ Upgrading equipment to ensure cleanability and sterility
✔ Improving material flows to prevent cross-contamination
2. Manufacturing and Quality Systems
Remediation CAPA actions might include:
✔ Updating automation systems to comply with data integrity requirements
✔ Improving deviation investigations to prevent repeated issues
✔ Strengthening CAPA verification procedures to measure real effectiveness
3. Regulatory Readiness
Remediation CAPA actions might include:
✔ Developing a structured training program to prevent repeat compliance errors
✔ Implementing quality system updates to improve document control and traceability
✔ Conducting mock inspections to test readiness before regulatory re-inspections
Executing the Plan: Ensuring Accountability
A successful remediation effort is not just about fixing findings but ensuring long-term compliance through structured execution and accountability.
Each corrective action should be measurable, verifiable, and sustainable, with clear follow-up mechanisms to ensure CAPAs remain effective.
The Quality Remediation Plan (QRP) should be regularly reviewed and updated as actions progress, with clear documentation to demonstrate compliance efforts to regulators.
Building a Compliance System That Lasts
The goal of remediation is not just to clear findings but to establish a proactive compliance culture that prevents future violations. By focusing on risk-based prioritization, targeted CAPAs, and structured execution, companies can move beyond reactive fixes and build stronger, more resilient GMP systems.
If your team is navigating a complex remediation effort, having the right strategy, execution plan, and compliance oversight can make all the difference. A structured, risk-based approach ensures you don’t just fix issues, you prevent them from happening again.
Key Takeaways
Some of the key takeaways from this post include:
Not All Compliance Gaps Are Equal
A risk-based approach ensures that the most critical compliance gaps are prioritized first to protect product quality and patient safety.
A Site-Approved Quality Remediation Plan (QRP) is Essential
This centralized plan defines remediation actions, timelines, responsibilities, and progress tracking, ensuring transparency for auditors.
Corrective Actions Must Be Sustainable
Temporary fixes won’t satisfy regulators. CAPA plans should address root causes, prevent recurrence, and be verified for effectiveness over time.
Facilities, Utilities, and Equipment Must Meet Compliance Standards
If outdated systems are introducing risk, upgrades to equipment, automation, and material flows should be part of the remediation effort.
Regulatory Readiness Must Be Proactive
Mock inspections, training programs, and improved data integrity controls help prevent repeated findings and improve overall compliance posture.
Next Steps
For a successful remediation project you should:
Assess your compliance gaps across your operation and quality systems. Ensure previous regulatory findings are fully remediated and use risk-based prioritization to focus on high-impact issues.
Develop a Quality Remediation Plan (QRP) with clear actions, timelines, and accountability to align with ICH Q9 principles.
Prioritize critical CAPAs such as improving material flows, upgrading utilities, and enhancing automation for data integrity.
Verify effectiveness, strengthen regulatory readiness, and prepare for audits with mock inspections and training programs.
If you looking for support for your remediation project, you should contact us to discuss your remediation needs and ensure long-term compliance. We would be happy to have a confidential chat.
Comments